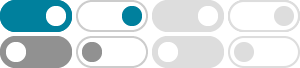
MPC vs PID – A Comprehensive Control Method Comparison
Among the myriad of control methods available, Model Predictive Control (MPC) vs Proportional-Integral-Derivative (PID) stand out as two competing strategies. In this article, we delve into the intricacies of each method, compare its strengths and weaknesses, explore applications, and provide insights on selecting the most suitable approach.
Temperature Control with the Use of PID - MathWorks
Dec 10, 2002 · This model shows a simulation of how temperature is controlled with the use of a PID (proportional-integral-derivative) controller.
Analysis of CSTR Temperature Control with PID, MPC & Hybrid MPC-PID …
Jan 1, 2022 · It has been observed that the hybrid MPC-PID has a more effective control action than a PID controller; with some tuning, the MPC controller can maintain the temperature within a...
This thesis examines the use of Model Predictive Control (MPC) compared to tra-ditional PID control. The purpose of the work is twofold: to enhance the under-standing of MPC in the industry and to investigate the possibility to improve the performance of a …
paper presents two controllers proportional, integral, and derivative control (PID) and model predictive control (MPC) for controlling the temperature of the reactor. Comparative analysis is being carried out between the two controllers. Effective temperature control is achieved by the use of model predictive control in terms of
This paper presents an analysis of the continuous stirred tank reactor (CSTR) temperature control with the Proportional-Integral-Derivative (PID) Controller, Model Predictive Controller (MPC) and Hybrid-Model Predictive Controller-Proportional Integral Derivative Controller (MPC-PID).
Practical Design and Application of Model Predictive Control
In this chapter a model predictive controller (MPC) will be used to control the active optical filter to achieve optimal output power based on PV module temperature. A PV module thermoelectrical model is introduced in Section 8.2 and is used as a testbed to demonstrate effectiveness.
MPC is an optimization-based control technique that uses:1) behavior over a given horizon, 2) an objective function that represents what systems behavior is desirable, 3) model structure also hinders the implementation of classical centralized or hierarchical control schemes.
controls - How do I integrate an MPC, PID and System models …
Oct 6, 2013 · Your PID-controller cannot be defined using this block, as Simulink requires a higher or equal order for the denumerator. Instead use the PID controller Block. You need to calculate the Proportional, Integral and Differential gain before.
A comparative study of MPC and optimised PID control
Jan 1, 2015 · The PID depends mainly on three terms, the P gain, I gain and lastly D gain for control each playing unique role while the MPC has more information used to predict and control a system.